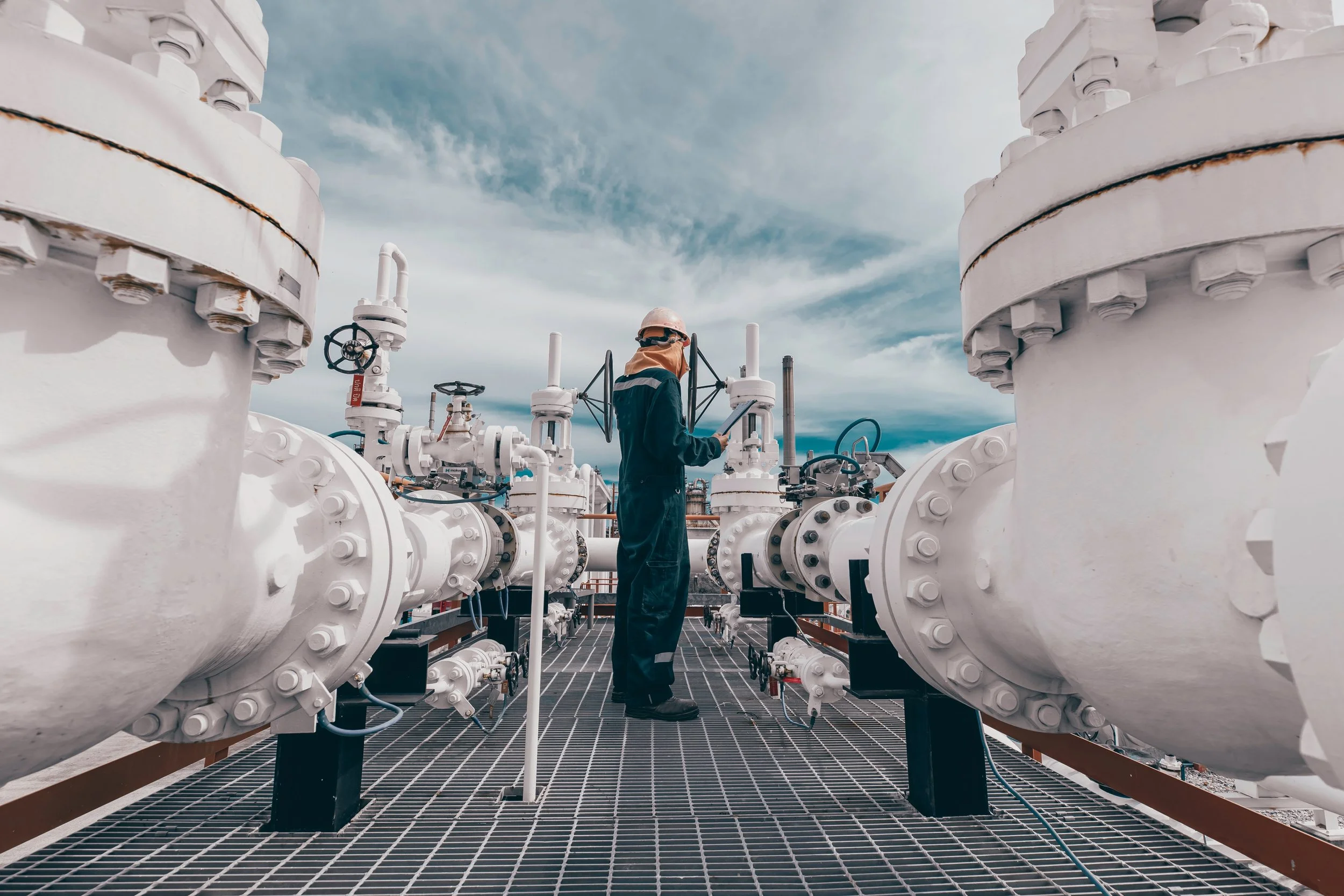
Debottlenecking & Optimization
Rangeland Engineering specializes in debottlenecking and optimization of oil and gas facilities, helping clients maximize throughput, efficiency, and reliability. Our team of experts identifies and addresses operational constraints, streamlines processes, and implements innovative solutions to unlock your facility's full potential. Whether it's enhancing production capacity, improving energy efficiency, or reducing downtime, we deliver tailored engineering strategies that drive measurable results. Partner with Rangeland to optimize your assets and achieve peak performance in today's competitive energy market.
Increase feed / production capacity by 5 to 30%
Operate at new feed composition or contaminant levels +/- 10 to 30%
key componentImprove overall or individual equipment thermal efficiency by 5 to 15%
Optimize product quality specifications to optimize product throughput
and commercial return from 1 to 5%Utilize feed-forward / feed-back process control schemes to maintain optimum,
continuous process control of key variables and key commercial metricsMonitor tower flooding conditions
Monitor thermal equipment fouling
Operations and EPCM control team to monitor operational and commercial performance daily
Conduct plant performance testing, match performance with process model (HYSYS), identify process pinch points for remediation
Detailed design, programming and commissioning of advanced process control strategies utilizing DCS and PLC systems
-
Project Diamond
Pembina engaged Rangeland to increase flow-through capacity of the original process train at their Redwater facility.
Our team evaluated the process conditions and ultimately recommended a combination of tower tray upgrades and reboiler modifications. The existing kettle type reboilers were replaced with vertical thermosyphon style requiring major infrastructure changes in both piping and structural elements. Significant hot oil system debottlenecking was required to provide the required heat duty including piping upgrades and system paralleling. Modular construction focus and a streamline integration is a key success in this project. Integrating the new equipment into the limited space was a complex endeavor; new reboiler equipment, in a new orientation, was a significant challenge to overcome
-
Asphaltene Removal and Plant De-Bottlenecking
Rangeland worked with the plant operations staff to develop an asphaltene removal and filtration for a 70 MBPD NGL Processing facility including filters, tanks, pumps and automotive switching controls.