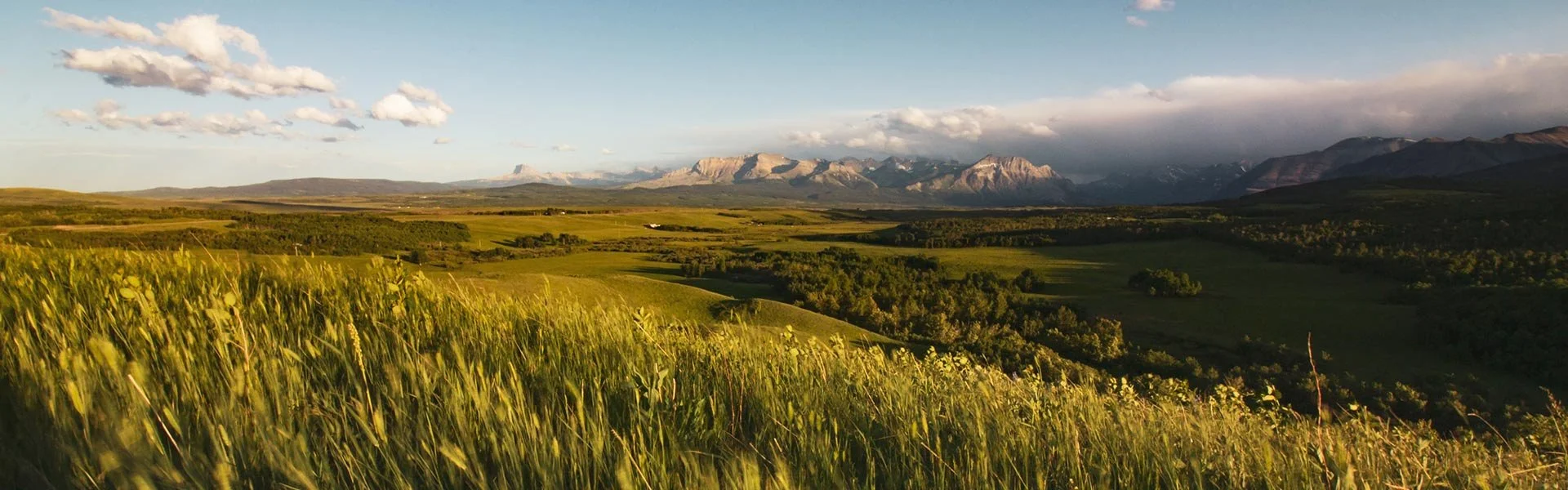
Salt Cavern Storage
We’ve raised the bar on salt cavern safety.
Salt caverns are essentially impermeable to hydrocarbons and provide a unique and cost effective option for large volume storage of NGLs (ethane, propane, butane and condensate) and crude oils. Rangeland has been in the business of salt cavern storage from our inception, while bringing decades of project development experience from our talented team of professionals. Most recently and over the past five years, Rangeland has supported the completion of more than 200+ salt caverns. Including Natural gas, Dense Phase Ethylene, C2, Propylene, C3, C4, NGL Mix, C5, Refined Oil Products, Crudes, and H2.
Rangeland has a dedicated engineering group that supports the complete design and development of caverns, brine ponds and related processing facilities all with system safety as paramount. Often faced with the challenge of handling volatile products under extreme pressures, we moved beyond ‘business as usual’ and worked with our clients to understand their specific issues and risks at hand. Our investments have paid off allowing our team to raise the bar for total system safety; across multiple product streams; across various elements of the whole storage facility.
In addition to specific in-house expertise, our team works closely with trusted partners to design all aspects of cavern storage systems including the engineering and mining of the cavern and the associated wellhead and tubular designs. Rangeland Engineering can provide geophysical assessments and detailed wash programs which are mated with customized wellbore designs. Collaborating on the sub-surface requirements Rangeland offers a fully integrated system design and provides the procurement services to complete the entirety of the work.
-
Pembina Salt Cavern Program
Design an interconnected series of salt caverns that allowed for handling of multiple products in plant feed service as well as finished product storage.
To support the cavern development, the program required a series of associated projects such as system manifolds, product drying and brine system upgrades.
Planning work included cavern development, geophysical assessment, cavern hydraulic performance modelling and system infrastructure. Detailed engineering included surface facilities, production conversion, system de-bottlenecking and integration into existing salt cavern storage and processing facilities.
A key challenge for Rangeland was to incorporate project changes required for the production-phase conversion as the needs, systems and scope sometimes shifted over the course of the two years in which the caverns were in wash phase.
The total program included:
• Eight new caverns encompassing 30 associated and supporting projects
• Hydraulic design and string-and-casing sizing for single, dual and triple cavern configurations
• Product injection pump systems (ethane, ethylene, propane, butane and NGL mix)
• Product treating facility including CaCl dryers, mole sieves, and brine separation
• Cavern wash infrastructure including river-water intake, wash-pump systems, disposal wells and temporary wash-phase facilities and systems
• Product, brine, flare and utility distribution systems, including strategically located, expandable, manifold setups
• Design engineering for custody metering, flow control, and safety shutdown systems -
Storage Caverns & Wellhead – up to 800 Mbbl
Rangeland has designed over 100 caverns and 50 surface facilities in Western Canada, working with multiple clients.
Facilities included hydraulic design, string and casing sizing for single, dual and triple completion cavern configurations.
The projects included:
• Brine ponds, brine distribution, product distribution, high pressure injection systems (2800 psig), disposal wells, treating systems, custody metering and all utilities.
• Integration into existing salt cavern facilities with 3 to 22 salt caverns and processing facilitiesProducts stored:
• C2+ and C3+ NGL FEED
• Ethane and ethylene product
• Propane and propylene product
• Butane and butylene product
• Condensate product
• 25-35 API gravity crude oil -
ROF Cavern 26
To support a new propane dehydrogenation facility, a new storage cavern for polymer grade propylene (PGP) was required. The development of the 100,000 m3 storage cavern progressed in three phases: wash phase, PGP cap fluid phase, and production phase.
The PGP cap phase was initiated to transition from condensate to PGP cap fluid due to contamination concerns in using condensate as a cap fluid to the stored PGP in production phase.
The total program included:
• Pre-FEED, FEED and Detailed engineering design
• Hydraulic design of downhole casing and string sizing
• Design and specification of high-pressure PGP cavern injection pumps
• Detailed design of the wellhead and safety systems
• Design of supply and delivery pipeline, metering and controls plus ancillary utilities